Tokamak Plasma Experiments
There are two existing facilities in the institute to do experiments related to fusion plasma, namely Aditya tokamak and Superconducting Steadystate Tokamak-I (SST-I). Recent developments in ADITYA-U include realization of plasma parameters close to the design values, deployment of a novel electromagnetic high-speed pellet injectors for the first time, experimental studies related to runaway electron generation and losses, toroidal rotation studies and modulation of drift tearing MHD modes. Continued technology improvements on SST-1 yielded, for the first time, a record 15 days of plasma operation with maximum ohmic pulse current durations of 650 ms, a good 200 ms improvement over the one obtained last year.
Aditya Tokamak
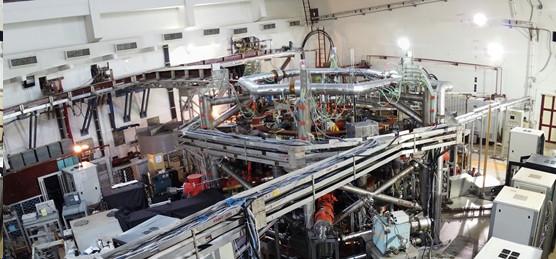
After 25 years of successful operation of ADITYA tokamak (~ 30,000 discharges) in a circular poloidal ring limiter configuration, it has been upgraded to a tokamak named ADITYA Upgrade (ADITYA-U) to realize the shaped-plasma operations in an open diverter configurations. The upgradation was conceptualized in the year 2014 and the ADITYA tokamak had been dismantled to its base level in the year 2015. The ADITYA-U tokamak construction was completed in the year 2016 and the first plasma was achieved in December 2016.
The ADITYA-U tokamak is a medium-size air-core tokamak with a major radius of 0.75me and a minor radius (limiter radius) of 0.25 m and maximum toroidal magnetic field of 1.5 T. It has a toroidal belt limiters and two quarter poloidal limiters at two toroidal locations made up of graphite. The ADITYA-U is designed to produce circular plasmas with plasma current ~ 150 – 250 kA, plasma duration of ~ 250 – 350 ms with a chord average electron density in the range of 1 – 5 x 10^19 per meter cube and electron temperature ~ 300 eV – 1000 eV. In addition, it is designed to achieve shaped plasmas with plasma current ~ 100 – 150 kA, elongation (k) ~ 1.1 - 1.2 and triangularity ~ 0.45.
Parameter
| Value
|
Major radius
| 75 cm
|
Minor radius
| 25 cm
|
Plasma current
| 180 kA
|
Coil type
| Normal Conducting, water cooled
|
Toroidal magnetic field
| 1.5 Tesla (Max)
|
Central solenoid
| Normal Conducting, water cooled
|
Plasma cross-section
| Circular
|
Plasma duration
| 250-300 milli seconds
|
External Heating
| ECRH, ICRH
|
Table The operational parameters of Aditya-U tokamak
Steadystate Superconducting Tokamak-1 (SST-1) 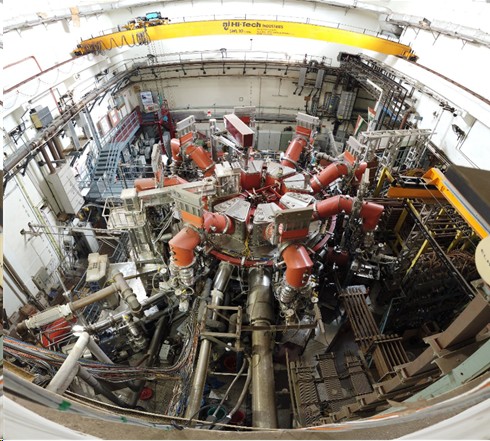
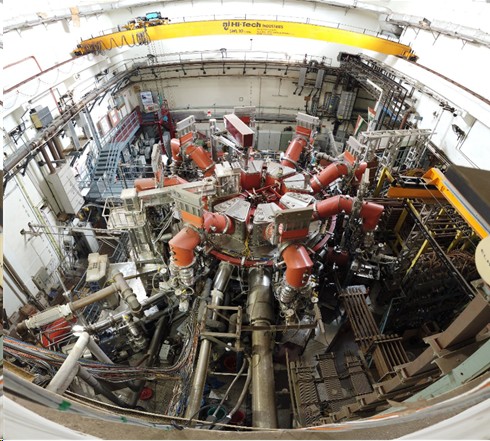
Steady-State Superconducting Tokamak (SST-1) is a medium size superconducting tokamak, which has been designed and built to study the physics of the plasma processes in tokamak under steady-state conditions. In recent times the experimental campaign has been extended to a record 15 days with 300 plasma shots, with plasma pulse durations upto 650 milliseconds, 30% higher than the best achieved ever before, and better reproducibility of plasma parameters. This became possible due to improvement of the initial magnetic field null inside the vacuum vessel, permitting higher gas fill pressures, in turn allowing plasma creation with a limited pulse of electron cyclotron heating at 42 GHz. The improved plasma density also permitted long-duration current drive using injected power at 3.7 GHz, which was not hitherto possible due to a low-quality plasma near the wave launcher. Also for the first time in SST-1, the three frequency ranges used for plasma heating (tens of MHz, few GHz, tens of GHz) were applied simultaneously. Improved cryo-insulation has permitted production of liquid Helium from the cryo-plant in addition to coil cooling, which will now allow cooling of current leads.
Parameter
| Value
|
Major radius
| 110 cm
|
Minor radius
| 20 cm
|
Plasma current
| 220 kA (Max)
|
Coil type
| Superconducting (4K)
|
Toroidal magnetic field
| 3 Tesla
|
Central solenoid
| Copper conductor
|
Plasma cross-section
| Elongated
|
Plasma duration
| ~650 milli seconds (as of March 2020) target ~ 1000sec
|
External current drive and heating
| LHCD, ECRH, ICRH
|
Table The operational parameters of SST-1 Tokamak
Cryogenic Systems for Steady State Superconducting Tokamak (SST-1)
Introduction
Cryogenic Systems of SST-1 has following sub-systems






1.3 kW at 4.5 K HRL consists of
A Compressor Skid housing 3 nos. of screw compressors
B Oil Removal System (ORS)
C On-line Purifier
D Coldbox with Main Control Dewar (MCD)
WGM System has 4 nos. of medium pressure storage vessels to store pure Helium gas and 2 nos. of high pressure storage vessels to store impure Helium gas.
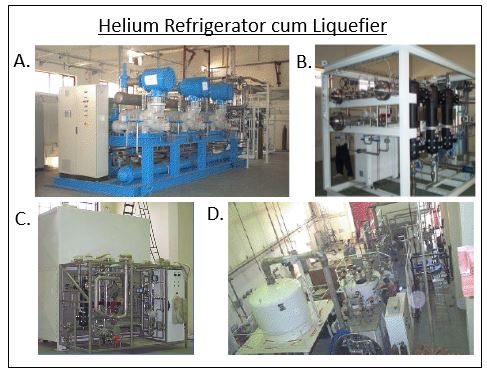
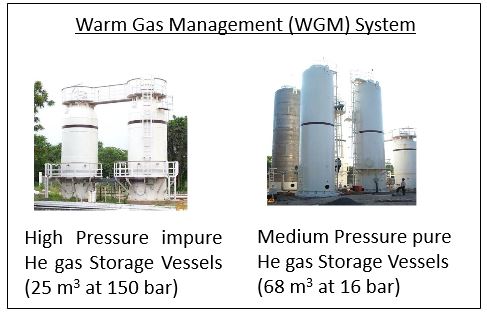
Recent Developments
1. Cryogenics system is used to cool the superconducting magnets of SST-1 Tokamak regularly and plasma experiments are conducted in SST-1 Tokamak.
2. Recently 2 pairs of conventional vapour cooled current leads have been installed inside Current Feeder System to charge the poloidal field -3 (PF-3) coils.
3. The PC3000 Programmable Process Controller of on-line purifier is replaced with Eurotherm’s T2750 Process Automation controller, as PC3000 system is being obsoleted.
4. The Citect based Supervisory Control & Data Acquisition System (SCADA) of HRL is replaced with Wonderware InTouch 2017 R2 based SCADA system.
5. Remote monitoring of HRL process parameter within IPR campus is accomplished using EPICS based web monitoring system.
6. The upgradation of SCADA systems of IFDCS, CFS, LN2 management and distribution system from Wonderware InTouch 9.5 to latest InTouch 2017 R2 system.
7. Regular preventive maintenance of HRL is carried out such as shaft alignment of helium screw compressor to it’s motor, filling of 400L BreoxTM oil in compressor skid, replacement of coalescor filter cartridges in Primary Oil Separator (POS) of compressor skid & Oil Removal System (ORS), calibration of process instrumentation etc.
8. Performance tests of HRL plant capacity in pure refrigeration (R) mode, pure liquefaction (L) mode and mixed (R+L) mode.
9. Hydrostatic testing of high and medium presser storage vessels as per Petroleum and Explosives Safety Organization (PESO) norms.
10. The Compressor Machine Conditioning Monitoring (MCM) System is developed to monitor temperature and vibration of electrical motors of Helium screw compressors.
Achievements


Recent Publications
1) Upgradation plans of SST-1 cryogenics system at IPR, V. Tanna, et. al., IOP Conference Series: Journal of Physics: Conference Series 823 (2017) 012002, doi: 10.1088/1742-6596/823/1/012002
2) Cryogenic process optimization for simultaneous cool down of the TF and PF superconducting coils of SST-1 Tokamak, P. Panchal, et. al., IOP Conf. Series.: Materials Science and Engineering 502 (2019) 012106 doi:10.1088/1757-899X/502/1/012106
3) Development of New SCADA for 1.3 kW Helium Refrigerator cum Liquefier at 4.5 K, P. Panchal, et. al., IPR/TR-609/2020
4) Report on Current Feeder System (CFS) for installation of PF3 Current Leads (CLs) along with associated cryogenic network towards producing Shaped Plasma in SST-1, A. Garg., et. al., IPR/TR- 610/2021
Indigenous developments of Current Leads for superconducting magnets:
Introduction : Any superconducting (SC) fusion device or SST-1 like machine demands extensive use of SC magnets, which excited at several kA through current leads (CLs) only. Even, they may consume ~ 25% of total operational costs of such fusion reactors.
Current Lead (CL) is an optimal device, which bridges a gap between Power supply (at room temperature) and NbTi superconducting coils at cryogenic temperatures (~ 4.5 K in SST-1). 10 kA rated vapour cooled current leads (VCCLS) have been designed, indigenously developed and tested under cryogenic conditions at the full rated current along with long pulse operations to fulfil the SST-1 requirements. Subsequently, total 10 pairs of VCCLs manufactured in-house at IPR for the operation of TF (toroidal field) and PF (poloidal field) coils. Currently, 01 pair is installed in the Current Feeder System to charge all 16 TF Magnets while 02 pairs for PF-3 magnets. The heat exchanger is one of the major section of the CL that is a bundle of Cu rods being accommodated by concentric stainless steel tube to allow the cryogen helium to have better heat transfer.
![]() | ![]() |
Recent Developments
An approximately 50% of 1.3 kW power of Helium Refrigerator cum Liquefier (HRL) commissioned at IPR is consumed only by existing VCCLs. With the advancement of technology, this significant capacity can be saved with the introduction of High Temperature Superconductor (HTS) instead of Nb-Ti. BISCO tapes as an HTS is selected due to its high critical temperature (110 K) i.e. above the boiling temperature of liquid nitrogen. Accordingly, liquid nitrogen will be utilized to cool this part as very economical solution instead of liquid helium. HTS CLs offer considerable 3 to 4 times economic benefit in the operation of superconducting magnets/fusion devices to achieve higher field. As a development activity, the design of HTS CL initiated at IPR and 3.3 kA rated one pair of HTS prototype CL was initially manufactured in the association with Indian Industry.
Therefore:




Indigenous developments of Current Leads for Superconducting magnets
Achievements
VCCLs




HTS CLs


Recent Publications
Report on Current Feeder System (CFS) for installation of PF3 Current Leads (CLs) along with associated Cryogenic Network towards producing shaped plasma in SST-1 [Technical Report: IPR/TR-610/2021, Jan 2021]
Atul Garg, H. Nimavat, P. Shah, R. Panchal, Srikanth L.N., G. Purwar, P. Biswas, H. Patel, F.S. Pathan, P. Thankey, D. Sonara, D. Christian, A. Panchal, N. Kumar, A. Prakash, U. Prasad, V.L. Tanna, B.R. Doshi, R. Srinivasan and D. Raju
Multichannel superinsulated Helium transfer line
Introduction: A multichannel superinsulated Helium transfer line has been developed in house and installed at SST-1 Cryogenic facility. This cryogenic transfer line is developed in order to have a dedicated supply line and return line of liquid helium for PF-3 and PF-5 coils. The length of this transfer line is approximately 10m which was integrated with flow distribution box of SST-1 Cryogenics facility and with port no 13 bottom of SST-1 tokamak at the other end. The internal process lines of the transfer line are wrapped with Multi layer insulation of optimum layer density and supported with G-10 at appropriate distance in order to have optimum heat leak. The transfer line will be under dynamic vacuum during operation in order to reduce the heat load due to residual gas conduction. Smooth bends are used wherever necessary and cryogenic compatible flexible hoses are used at both ends of the process pipes for connecting with interfacing systems.
![]() | ![]() |



Programmable Switch Mode Power Supply
Introduction:


1) Harmonic Filter
2) Mains input rack
3) Central Electronics Controller Unit (CCU)
4) 8 nos. of Sub-converters
5) Direct Current Current Transformer (DCCT)
6) Water-cooled cables



![]() Architecture of 12 kA DC Power Supply
| ![]() |
Recent Developments

and acceptance test.
![]() Rated Current during Constant Current (CC) Mode
| ![]() Rated Voltage during Constant Voltage (CV)
Mode
|

as High Temperature Superconductors (HTS) and copper heat exchanger in September 2016.
Approximately, 950 A current had provided by this power supply.


up to 1,000 A using the power supply in February 2022.

Recent Publications
1) Experience of 12 kA / 16 V SMPS during the HTS Current Leads Test, P. Panchal et. al., IOP Conference Series: Journal of Physics: Conference Series 823 (2017) 012006, doi:10.1088/1742-6596/823/1/012006
2) Design and development of water-cooled dummy load for 12 kA, 16 V Power Supply test at IPR, D. Christian, et. al., Poster presentation at 27th PSSI
A Small-Scale Spherical Tokamak (SSST) is under construction to study the plasma initiation and non-inductive current drive. This will help to realize a volumetric neutron source. The project is expected to go for plasma opertation in the 2nd Qtr. 2022.
- ADITYA-U
- SST1
- SSST